Difference between revisions of "SatNOGS Rotator Controller"
(→Firmware and Pin Assignments) |
m (→DC motor driver: Warning to not accidently solder in the 100uF capacitors as these can fail with the DC motors. On mine they shorted the power supply.) (Tag: Visual edit) |
||
(100 intermediate revisions by 14 users not shown) | |||
Line 3: | Line 3: | ||
|image= Rotator controller v2.jpg | |image= Rotator controller v2.jpg | ||
|type= Rotator Controller for SatNOGS rotator. | |type= Rotator Controller for SatNOGS rotator. | ||
− | |cost= | + | |cost= 60-80€ |
|status= Working | |status= Working | ||
− | |latest-release-name= | + | |latest-release-name= - |
− | |latest-release= v2 | + | |latest-release= v2.3 |
− | |source-repo= https:// | + | |source-repo= [https://gitlab.com/librespacefoundation/satnogs/satnogs-rotator-controller satnogs-rotator-controller - GitLab] |
+ | [https://gitlab.com/librespacefoundation/satnogs/satnogs-rotator-controller-encoder satnogs-rotator-controller-encoder - GitLab] | ||
|documentation= https://wiki.satnogs.org/index.php?title=SatNOGS_Rotator_Controller SatNOGS wiki | |documentation= https://wiki.satnogs.org/index.php?title=SatNOGS_Rotator_Controller SatNOGS wiki | ||
}} | }} | ||
− | == | + | ==Introduction== |
SatNOGS Rotator Controller refers to the set of electronics designed to operate a SatNOGS Rotator. There have been multiple iterations of the rotator controller design, but the modularity of the approach enables operations between different versions of the controller and the rotator. | SatNOGS Rotator Controller refers to the set of electronics designed to operate a SatNOGS Rotator. There have been multiple iterations of the rotator controller design, but the modularity of the approach enables operations between different versions of the controller and the rotator. | ||
Since the start of 2016, the rotator controller design is able to facilitate a DC-motors or stepper-motors rotator design. We intend to keep this modularity for the electronics and firmware design to facilitate the variety of build by our community. | Since the start of 2016, the rotator controller design is able to facilitate a DC-motors or stepper-motors rotator design. We intend to keep this modularity for the electronics and firmware design to facilitate the variety of build by our community. | ||
− | == Rotator Controller v2 == | + | ==Rotator Controller v2== |
<gallery> | <gallery> | ||
− | + | Pcb_schema_v2_revC.png | |
− | + | Pcb_board_v2_revC.png | |
</gallery> | </gallery> | ||
The PCB are tested in this [https://network.satnogs.org/stations/9/ ground station]. | The PCB are tested in this [https://network.satnogs.org/stations/9/ ground station]. | ||
− | === Features === | + | ===Features=== |
− | |||
− | |||
− | |||
− | |||
− | |||
− | |||
− | |||
− | |||
− | |||
− | |||
− | |||
− | |||
− | + | *It is designed to fit the entire electronics needed to control rotator in Euroboard 80x50 mm. | |
− | * | + | *Main micro-controller is [https://store.arduino.cc/arduino-pro-mini Arduino pro-mini], [https://github.com/sparkfun/Arduino_Pro_Mini_328 SparkFun's Arduino Pro Mini 328] dev-board with ATmega328p. |
− | * | + | *The modular design includes plug-in either [https://www.pololu.com/product/2133 DRV8825]/[https://www.pololu.com/product/1182 A4988] or [https://www.pololu.com/product/1213/resources DC motor drivers] (MC33926). |
− | * | + | *The power supply in embed in the same board in contrast with previous version. |
− | * | + | *Filtered power supply of micro controller. |
− | * | + | *An I2C multiplexer is used to connect I2C encoders AS5601 (same ID) to get position feedback for each axis. |
− | * | + | *A temperature sensor TC-74 monitoring the temperature inside the controller box in order to protect them from over-heating. |
+ | *There are some spare dev-pins in order to connect other peripherals like IMU or an LCD display. | ||
+ | *Pins with integrated RC-Low Pass filter for end-stops connection. | ||
+ | *Default communication interface is RS-485 but it can also be used as a UART. | ||
+ | *Using different paths for digital and power (motors) GND. | ||
+ | *Electrolytic capacitor and TVS-diode in PSU input | ||
+ | *Flashed either by using UART or ISP header | ||
+ | ===Build sequence=== | ||
− | ==== | + | *Make sure you have a [[SatNOGS Rotator v3|mechanical assembly]] of the rotator constructed and ready |
+ | *Buy the PCB. [https://oshpark.com OshPark],[https://www.seeedstudio.com/fusion_pcb.html Seeed Fusion][https://www.pcbway.com PCBWay.com], [http://dirtypcbs.com DirtyPCBs.com], [https://www.elecrow.com/ Elecrow], [https://www.makerfabs.com Makerfabs] have been used in the past with good results. | ||
+ | **You can order the v2.2 of the board directly using [https://oshpark.com/shared_projects/w0s8d4OJ this OSHPark link] | ||
+ | **You can order the v1.0 of the rotary encoder board using [https://oshpark.com/shared_projects/I3b8SCci this OSHPark link] | ||
+ | **You can order PCB as well as [https://www.seeedstudio.com/prototype-pcb-assembly.html PCB Assembly service] from Seeed Studio | ||
+ | *Get all the necessary components according to BOM from latest tag (or the version that you want to build), [https://gitlab.com/librespacefoundation/satnogs/satnogs-rotator-controller/tags Gitlab Tags] | ||
+ | *Assemble the PCB, by soldering the components | ||
+ | *Burn the firmware | ||
+ | *Using the wiring diagram, connect the controller to the Rotator | ||
+ | *You are ready! Proceed with testing | ||
+ | |||
+ | |||
+ | ====Assembly Guide==== | ||
+ | |||
+ | [[File:C1000-1 enclosure pcb mount.png|thumb|center|800x420px|alt=|FDM-3Dprinted, Material: ABS, Layer height: 0.4 mm, Perimeters: 2, Top/bottom solid layers: 3, Fill density: 20%, Fill pattern: Honeycomb, Fan speed: [35, 100], No support material]] | ||
+ | [[File:H1000_aluminium_enclosure.png|thumb|center|800x420px|alt=|Rotator Controller - Drill holes]] | ||
+ | [[File:Rotator_controller_sheet1.png|thumb|center|800x420px|alt=|Rotator Controller sheet 1/2]] | ||
+ | [[File:Rotator_controller_sheet2.png|thumb|center|800x420px|alt=|Rotator Controller sheet 2/2]] | ||
+ | |||
+ | ====Microcontroller==== | ||
+ | <gallery mode="packed" heights="250px"> | ||
+ | Uc.png|Microcontroller | ||
+ | Uc_orientation.png|Microcontroller Orientation | ||
+ | I2c_pullup.png|I2C pull-up resistors | ||
+ | </gallery> | ||
+ | <!-- changed at feb.25th 2018 | ||
+ | {| | ||
[[File:Uc.png|thumb|320x240px|Microcontroller]] | [[File:Uc.png|thumb|320x240px|Microcontroller]] | ||
+ | | | ||
[[File:Uc_orientation.png|thumb|320x240px|Microcontroller Orientation]] | [[File:Uc_orientation.png|thumb|320x240px|Microcontroller Orientation]] | ||
− | [[File:I2c_pullup.png|thumb|320x240px|I2C pull-up resistors]] | + | | |
+ | [[File:I2c_pullup.png|thumb|320x240px|I2C pull-up resistors|left]] | ||
+ | |} | ||
+ | <br clear="all"/>--> | ||
− | + | The main micro-controller of the board is arduino pro-mini 5V@16MHz, ATmega328P. | |
+ | The +5V of the controller are produced from arduino pro-mini. | ||
+ | Some clones do not use correct parts in LDO, like the original one, with | ||
+ | result, when it powers up with +12V, burned. | ||
− | + | Some examples, | |
− | |||
− | |||
− | |||
− | + | *[https://community.libre.space/t/v2-controller-board-magic-smoke/1878 SatNOGS Community] | |
− | * | + | *[http://westsideelectronics.com/blew-up-a-cheap-arduino-pro-mini-clone/ West Side Electronics] |
− | * | ||
− | + | One Solution is not use clones, use [https://www.sparkfun.com/products/11113# Sparkfun's arduiuno pro-mini 5V@16MHz, ATmega328P]. | |
− | + | The second solution is to add a LDO, like [https://gr.mouser.com/datasheet/2/268/mic5205-778789.pdf MIC5205] (maybe in a new revision of v2). | |
− | The | + | The power consumption in +5V is: |
− | |||
− | |||
− | |||
− | |||
− | |||
− | |||
− | |||
− | + | {| class="wikitable" | |
− | + | |- | |
− | + | !- | |
− | + | !QTY. | |
− | + | !VCC(V) | |
− | + | !IDD(mA) | |
− | + | !Total(mA) | |
− | + | |- | |
+ | |AS5601 | ||
+ | |2 | ||
+ | |5 | ||
+ | |6.5 | ||
+ | |13 | ||
+ | |- | ||
+ | |PCA9540B | ||
+ | |1 | ||
+ | |5 | ||
+ | |0.1 | ||
+ | |0.1 | ||
+ | |- | ||
+ | |SN65HVD485E | ||
+ | |1 | ||
+ | |5 | ||
+ | |2 | ||
+ | |2 | ||
+ | |- | ||
+ | |TC74 | ||
+ | |1 | ||
+ | |5 | ||
+ | |0.35 | ||
+ | |0.35 | ||
+ | |- | ||
+ | |arduino pro mini | ||
+ | |1 | ||
+ | |5 | ||
+ | |20 | ||
+ | |20 | ||
+ | |- | ||
+ | |MC33926 | ||
+ | |2 | ||
+ | |5 | ||
+ | |0.2 | ||
+ | |0.4 | ||
+ | |- | ||
+ | |DRV8825 | ||
+ | |2 | ||
+ | |5 | ||
+ | |0.1 | ||
+ | |0.2 | ||
+ | |} | ||
− | + | The LDO MIC5205 guaranteed 150mA output, for Stepper motors ~35-40mA, for DC motors ~35-40mA. | |
− | ==== Motor Drivers ==== | + | ====Motor Drivers==== |
− | ===== Stepper motor driver ===== | + | =====Stepper motor driver===== |
[[File:Stepper_2.png|thumb|320x240px|Stepper motor driver]] | [[File:Stepper_2.png|thumb|320x240px|Stepper motor driver]] | ||
[[File:Stepper_1.png|thumb|320x240px|Jumpers]] | [[File:Stepper_1.png|thumb|320x240px|Jumpers]] | ||
[[File:Stepper_orientation.jpg|thumb|320x240px|Orientation]] | [[File:Stepper_orientation.jpg|thumb|320x240px|Orientation]] | ||
− | For the stepper motor driver 2 options | + | For the stepper motor driver 2 options have been tested, [https://www.pololu.com/product/2133 DRV8825] and [https://www.pololu.com/product/1182 A4988]. |
For both options it is necessary to solder: | For both options it is necessary to solder: | ||
− | |||
− | |||
− | |||
− | |||
− | |||
− | + | *2 electrolytic capacitors C3, C4 100uF | |
− | * | + | *4 single 0.1" male connectors for U3, U4 |
− | * | + | *2 fixed terminal blocks P7, P8, Amphenol-VI0421550000G |
− | * | + | *6 jumpers to adjust the micro-step, '''default option is Full Step''' |
+ | Note: [https://hackaday.com/2016/08/29/how-accurate-is-microstepping-really/ Guide for microstepping selection] | ||
{| {{table}} | {| {{table}} | ||
− | | | + | | style="background:#f0f0f0;" align="center" |'''JP3/JP6''' |
− | | | + | | style="background:#f0f0f0;" align="center" |'''JP2/JP5''' |
− | | | + | | style="background:#f0f0f0;" align="center" |'''JP1/JP4''' |
− | | | + | | style="background:#f0f0f0;" align="center" |'''Microstep Resolution''' |
|- | |- | ||
− | | | + | | style="background:#f0f000;" align="center" |'''Low'''|| style="background:#f0f000;" align="center" |'''Low'''|| style="background:#f0f000;" align="center" |'''Low'''|| style="background:#f0f000;" align="center" |'''Full step''' |
|- | |- | ||
− | | align="center"|'''High''' || align="center"|'''Low''' || align="center"|'''Low''' || align="center"|'''Half step''' | + | | align="center" |'''High'''|| align="center" |'''Low'''|| align="center" |'''Low'''|| align="center" |'''Half step''' |
|- | |- | ||
− | | align="center"|'''Low''' || align="center"|'''High''' || align="center"|'''Low''' || align="center"|'''1/4 step''' | + | | align="center" |'''Low'''|| align="center" |'''High'''|| align="center" |'''Low'''|| align="center" |'''1/4 step''' |
|- | |- | ||
− | | align="center"|'''High''' || align="center"|'''High''' || align="center"|'''Low''' || align="center"|'''1/8 step''' | + | | align="center" |'''High'''|| align="center" |'''High'''|| align="center" |'''Low'''|| align="center" |'''1/8 step''' |
|- | |- | ||
− | | align="center"|'''Low''' || align="center"|'''Low''' || align="center"|'''High''' || align="center"|'''1/16 step''' | + | | align="center" |'''Low'''|| align="center" |'''Low'''|| align="center" |'''High'''|| align="center" |'''1/16 step''' |
|- | |- | ||
− | | align="center"|'''High''' || align="center"|'''Low''' || align="center"|'''High''' || align="center"|'''1/32 step''' | + | | align="center" |'''High'''|| align="center" |'''Low'''|| align="center" |'''High'''|| align="center" |'''1/32 step''' |
|- | |- | ||
− | | align="center"|'''Low''' || align="center"|'''High''' || align="center"|'''High''' || align="center"|'''1/32 step''' | + | | align="center" |'''Low'''|| align="center" |'''High'''|| align="center" |'''High'''|| align="center" |'''1/32 step''' |
|- | |- | ||
− | | align="center"|'''High''' || align="center"|'''High''' || align="center"|'''High''' || align="center"|'''1/32 step''' | + | | align="center" |'''High'''|| align="center" |'''High'''|| align="center" |'''High'''|| align="center" |'''1/32 step''' |
|- | |- | ||
|} | |} | ||
− | ===== DC motor driver ===== | + | *Do'''NOT''' solder 2 resistors 100k, R4, R7 in default configuration (full step) |
− | The DC motor controller is [https://www.pololu.com/product/1213 Dual MC33926 Motor Driver Carrier ] | + | *If you have A4988 for stepper motor drive and you want to use micro stepping, when the MS1 is HIGH |
+ | |||
+ | it is necessary to solder R4, R7 according to [https://www.pololu.com/product/1201 A4983 Stepper Motor Driver Carrier, Step (and microstep) size]. | ||
+ | |||
+ | In case of DRV8825, all pins MS1, MS2, MS3 have internal pull-up resistor. | ||
+ | |||
+ | Also it is necessary to update the definitions in [https://gitlab.com/librespacefoundation/satnogs/satnogs-rotator-firmware/blob/master/stepper_motor_controller/stepper_motor_controller.ino firmware], according to microstepping selection. | ||
+ | Example: | ||
+ | |||
+ | *Step Angle: 1.8 deg | ||
+ | *Microstep: 1/8 step | ||
+ | *Steps per Revolution: (360/1.8)*8 = 1600 | ||
+ | |||
+ | That means: | ||
+ | |||
+ | #define MICROSTEP 8 ///< Set Microstep | ||
+ | #define MAX_SPEED 6400 ///< In steps/s, consider the microstep | ||
+ | #define MAX_ACCELERATION 1600 ///< In steps/s^2, consider the microstep | ||
+ | #define SPR 1600L ///< Step Per Revolution, consider the microstep | ||
+ | |||
+ | It is necessary to change the maximum speed and acceleration according to new SPR. | ||
+ | |||
+ | An example: | ||
+ | |||
+ | The speed = 300steps/s and acceleration = 100steps/s^2 with | ||
+ | |||
+ | *1.8 deg/step stepper motor | ||
+ | *full step | ||
+ | *gear ratio 54 | ||
+ | |||
+ | means speed = 10deg/s and acceleration = 3.3deg/s^2 according to this [https://gitlab.com/librespacefoundation/satnogs/satnogs-rotator-firmware/blob/master/stepper_motor_controller/stepper_motor_controller.ino#L224 function]. | ||
+ | |||
+ | Be careful: | ||
+ | |||
+ | *[http://reprap.org/wiki/Pololu_stepper_driver_board adjust the current (current limiting) for stepper motors] | ||
+ | *add a heat-sink. | ||
+ | *plug the stepper motor drivers | ||
+ | |||
+ | The stepper motor that is used, is [https://www.omc-stepperonline.com/hybrid-stepper-motor/nema-17-bipolar-59ncm-84ozin-2a-42x48mm-4wires-w-1m-cable-and-connector-17hs19-2004s1.html Nema 17 Bipolar 59Ncm], | ||
+ | |||
+ | *Size: ▱42 x 48 mm | ||
+ | *Weight: 390 g | ||
+ | *Shaft diameter: 5 mm | ||
+ | *Step Angle: 1.8 deg | ||
+ | *Nominal speed @ 12V: 720deg/s | ||
+ | *Rated Current/phase: 2.0A | ||
+ | *Stall torque @ 12V: 0.59Nm | ||
+ | |||
+ | =====DC motor driver===== | ||
+ | [[File:Dc_motor_driver.png|thumb|320x240px|DC motor driver]] | ||
+ | |||
+ | It is necessary to solder: | ||
+ | |||
+ | *Solder U6 with 0.1" female connectors as shown in picture | ||
+ | *Solder 2 pads in yellow circle by using ~1mm diameter wire | ||
+ | *Solder 2 2-pin 3.5mm terminal blocks for 2 DC motors | ||
+ | |||
+ | Make sure you have not soldered the 2 electrolytic capacitors C3, C4 100uF. Those are only needed for the stepper motors. They can be destroyed by the DC motors and cause a short circuit of the power supply. | ||
+ | |||
+ | The DC motor controller is [https://www.pololu.com/product/1213 Dual MC33926 Motor Driver Carrier] | ||
+ | |||
+ | *Motor driver: MC33926 | ||
+ | *Motor channels: 2 | ||
+ | *Minimum operating voltage: 5V | ||
+ | *Maximum operating voltage: 28V | ||
+ | *Operating voltage: 12V | ||
+ | *Continuous output current per channel: 2.5A | ||
+ | *Current sense: 0.525 V/A | ||
+ | *Maximum PWM frequency: 20 kHz | ||
+ | *Operating PWM frequency: 3921.5Hz (~4kHz) | ||
+ | *Minimum logic voltage: 2.5V | ||
+ | *Operating logic voltage: 5V | ||
+ | *Maximum logic voltage: 5.5V | ||
+ | |||
+ | The DC motor that we use is [https://www.pololu.com/product/1104 50:1 Metal Gearmotor 37Dx54L mm], | ||
+ | |||
+ | *Size: 37D x 54L mm | ||
+ | *Weight: 195 g | ||
+ | *Shaft diameter: 6 mm | ||
+ | *Free-run speed @ 12V: 200 rpm | ||
+ | *Free-run current @ 12V: 300 mA | ||
+ | *Stall current @ 12V: 5000 mA | ||
+ | *Stall torque @ 12V: 1.2Nm | ||
+ | |||
+ | <br clear="all" /> | ||
+ | |||
+ | ====Communication==== | ||
+ | Note: For both options the firmware is the same. | ||
− | + | {{Warning |When the power supply (or PoE) of Raspberry Pi isn't good isolated (R ~7MΩ) with the main PSU (48V@1A) and the RS-485/UART loses packages, the ground of Raspberry Pi must be connected to the main ground of rotator (ground star).}} | |
− | |||
− | |||
− | |||
− | |||
− | |||
− | |||
− | |||
− | |||
− | |||
− | |||
− | |||
− | |||
− | + | =====''UART''===== | |
− | ===== ''UART'' ===== | ||
[[File:Jumper.png|thumb|320x240px|UART Jumpers]] | [[File:Jumper.png|thumb|320x240px|UART Jumpers]] | ||
[[File:Rs 485.png|thumb|320x240px|Pin Header]] | [[File:Rs 485.png|thumb|320x240px|Pin Header]] | ||
To use UART: | To use UART: | ||
− | |||
− | |||
− | |||
− | |||
− | ===== ''RS-485'' ===== | + | *solder JP7 and JP8 |
− | + | *solder pin header 0.1" female connector | |
+ | *not solder C1, U2, R18, R19 R9, R8, R1, D3 | ||
+ | *A is TX and B is RX | ||
+ | |||
+ | =====''RS-485''===== | ||
+ | [[File:RS485_solder.png|thumb|320x240px|RS485]] | ||
+ | [[File:Missing_rs485_r19.png|thumb|320x240px|RS485]] | ||
− | + | To use RS485: | |
− | ==== Power Supply ==== | + | *solder pin header 0.1" female connector |
+ | *solder C1, U2, R18, R19 R9, R8, R1, D3 | ||
+ | *not solder JP7 and JP8 | ||
+ | |||
+ | If you use PCB without R19 footprint, you can add it in arduino pro-mini UART header. | ||
+ | |||
+ | <br clear="all" /> | ||
+ | |||
+ | ====Power Supply==== | ||
[[File:Psu.png|thumb|320x240px|Power Supply]] | [[File:Psu.png|thumb|320x240px|Power Supply]] | ||
− | + | Recommended power supply for rotator controller is: 48V @ 1A DC. | |
+ | A good choice is the [https://gr.mouser.com/ProductDetail/709-LRS50-48 MEAN WELL LRS-50-48] | ||
− | + | The switching power supply could get as input voltage, 19-60V DC.<br> | |
− | + | In different input voltages, must be change the components like D4 and F1.<br> | |
+ | Default PCB components works at 48VDC. | ||
+ | |||
+ | <br clear="all" /> | ||
+ | |||
+ | ====Endstops==== | ||
+ | [[File:Endstop_part.png|thumb|320x240px|Endstop Specification]] | ||
[[File:Endstop.jpg|thumb|320x240px|Endstop]] | [[File:Endstop.jpg|thumb|320x240px|Endstop]] | ||
− | <br clear="all"/> | + | In reference design, mechanical endstops (the [https://www.aliexpress.com/item/10PCS-MICROSWITCH-LIMIT-SWITCH-3pin-N-O-N-C-MICRO-SWITCH-free-shipping/32692144896.html?spm=2114.search0104.8.13.2f3c2457pmCyFH&transAbTest=ae803_5&priceBeautifyAB=0 P/N SS0505] of endstop is specified in [https://gitlab.com/librespacefoundation/satnogs/satnogs-rotator satnogs rotator BOM]) , are used. |
+ | |||
+ | The controller has the capability to accommodate optical or magnetic endstop which connected to | ||
+ | P2 header with silkscreen, SW1, SW2, +5V and GND. | ||
+ | |||
+ | Mechanical endstops are connected to | ||
+ | |||
+ | *SW1 and GND for azimuth axis | ||
+ | *SW2 and GND for elevation axis | ||
+ | |||
+ | |||
+ | <br clear="all" /> | ||
+ | |||
+ | ====Encoders==== | ||
+ | Source files: [https://gitlab.com/librespacefoundation/satnogs/satnogs-rotator-controller-encoder satnogs-rotator-controller-encoder - GitLab] Firmware: [https://gitlab.com/librespacefoundation/satnogs/satnogs-rotator-firmware/blob/master/libraries/as5601.h satnogs-rotator-firmware - GitLab] | ||
− | |||
For stepper motor setup is optional (AS5601 encoder). | For stepper motor setup is optional (AS5601 encoder). | ||
− | + | For DC motor setup is necessary.[[File:Encoder_sheet1.png|thumb|center|800x420px|alt=|Rotary Encoder sheet 1/2]][[File:Encoder_sheet2.png|thumb|center|800x420px|alt=|Rotary Encoder sheet 2/2]]Fabrication files are placed in latest tag of [https://gitlab.com/librespacefoundation/satnogs/satnogs-rotator-controller-encoder satnogs-rotator-controller-encoder - GitLab]. | |
+ | <br /> | ||
+ | [[File:Encoder-case-3DP.png|center|thumb|583x583px|'''Parts''': C1010-1_encoder_case, C1011-1_encoder_case FDM-3Dprinted, C1012-1_magnet_mount, C1013-1_encoder_gear, '''Material''': ABS, '''Layer height''': 0.4 mm, '''Perimeters''': 2, '''Top/bottom solid layers''': 3, '''Fill density''': 20%, '''Fill pattern''': Honeycomb, '''Fan speed''': [35, 100], '''Generate support materia'''l (options of it depends of 3D printer).]] | ||
+ | |||
+ | |||
+ | |||
+ | <br /> | ||
+ | ===Firmware and Pin Assignments=== | ||
+ | |||
+ | =====Firmware===== | ||
+ | |||
+ | [https://gitlab.com/librespacefoundation/satnogs/satnogs-rotator-firmware For stepper motors] <br> | ||
+ | [https://gitlab.com/librespacefoundation/satnogs/satnogs-rotator-firmware For DC motors, thanks to] [https://github.com/ph4as ph4as] | ||
+ | |||
+ | =====Pins Configuration===== | ||
+ | This configuration is from the latest release in [https://gitlab.com/librespacefoundation/satnogs/satnogs-rotator-controller/tags Rotator Controller repository] | ||
+ | |||
+ | *M1IN1 10, Step or PWM1 | ||
+ | *M1IN2 9, Direction or PWM2 | ||
+ | *M1SF 7, Status flag | ||
+ | *M1FB A1, Load measurment | ||
+ | |||
+ | *M2IN1 11, Step or PWM1 | ||
+ | *M2IN2 3, Direction or PWM2 | ||
+ | *M2SF 6, Status flag | ||
+ | *M2FB A0, Load measurment | ||
+ | |||
+ | *MOTOR_EN 8, Enable/Disable motors | ||
+ | |||
+ | *SW1 5, Endstop for axis 1 | ||
+ | *SW2 4, Endstop for axis 2 | ||
+ | |||
+ | *RS485_DIR 2, RS485 Half Duplex direction pin | ||
+ | |||
+ | *SDA_PIN 3, Data I2C pin | ||
+ | *SCL_PIN 4, Clock I2C pin | ||
+ | |||
+ | *PIN12 12, Digital output pin | ||
+ | *PIN13 13, Digital output pin | ||
+ | *A2 A2, Analog input pin | ||
+ | *A3 A3, Analog input pin | ||
+ | |||
+ | <br clear="all" /> | ||
− | + | ===Pre-Flight Check=== | |
− | = | + | [[File:Pcb_testing_points.png|thumb|center|800x420px|alt=|Testing Points]] |
− | + | *Power your PCB with 48VDC, without plug-in arduino pro-mini and motor drivers, measure with multimeter the voltage in point 1. Expected voltage +12V (reference to GND). | |
+ | *Plug arduino pro-mini and measure with multimeter the voltage in point 2. Expected voltage +5V (reference to GND). | ||
+ | *Plug motor drivers (for steppermotors ensure the current is adjusted properly) | ||
+ | *Connect all peripheral devices like motors, sensors, endstops | ||
− | + | If the two first steps fail, something is wrong (maybe there is a short circuit) in PCB. Check the connections with a multimeter. | |
− | + | Then the board is ready to run the firmware, [https://gitlab.com/librespacefoundation/satnogs/satnogs-rotator-firmware/blob/master/README.md satnogs-rotator-firmware]. | |
− | + | <br clear="all" /> | |
− | + | ===Wiring=== | |
− | + | The silkscreen of PCB shows where the end-stops, rotary encoders, motors and communication interface are connected. For example SW1 is referred to azimuth end-stop, I2C-1 to elevation rotary encoder and M1 to azimuth motor. An example of wiring with [https://wiki.satnogs.org/SatNOGS_Rotator_v3#Cover_Box_-_Cabling SatNOGS Rotator v3]. | |
− | + | ===Troubleshooting hints=== | |
− | |||
− | |||
− | |||
− | + | As soon as the board is powered up or reset, it will auto-home, on first build you can trigger a reset multiple time or move the homing ring to get it "home". | |
− | |||
− | |||
− | |||
− | + | [https://gitlab.com/librespacefoundation/satnogs/satnogs-rotator-firmware/blob/master/README.md Connecting directly to the Arduino pro-mini] you will need to use 19200 bauds and "newline" line ending. | |
− | + | Here is some commands (took from [https://gitlab.com/librespacefoundation/satnogs/satnogs-rotator-firmware#easycomm-implemantation]) you can issue in the terminal emulator of your choice to test things: | |
− | |||
− | + | *'''VE''', it will returns something like "SatNOGS-v2.0" | |
+ | *'''RESET''', move to home position | ||
+ | *'''AZxx''', '''ELxx''', move to specified position (number) | ||
− | + | Nothing moves ? Look at the status and error register : | |
− | |||
− | + | *'''GS''', status register : 1 idle, 2 moving, 4 pointing, 8 error | |
− | + | *'''GE''', error register : 1 no error, 2 sensor, 4 homing, 8 motor, 12 over temperature, 16 watch dog timer interrupt | |
− | |||
− | |||
+ | By example, at first start, you might be in '''GS8''' and '''GE4''' until you get a good homing position for the rotator to start working. | ||
− | + | If you using an unreleased version of the board (the board that has fuse holder), in [https://community.libre.space/t/stepper-motor-issue/2438/2 community post] you can find pin configuration file. | |
− | = | + | <br clear="all" /> |
− | |||
− | + | ==Rotator Controller v1== | |
− | = | + | <br clear="all" /> |
− | + | [[Category:Hardware]] | |
+ | [[Category:Build]] | ||
+ | [[Category:Rotator]] |
Latest revision as of 00:55, 2 September 2021
SatNOGS Rotator Controller | |
---|---|
Information | |
Type: | Rotator Controller for SatNOGS rotator. |
Cost: | 60-80€ |
Release Information | |
Status: | Working |
Latest Release: | [v2.3 -] |
Repository: | [satnogs-rotator-controller - GitLab |
Documentation: | SatNOGS wiki |
Contents
Introduction
SatNOGS Rotator Controller refers to the set of electronics designed to operate a SatNOGS Rotator. There have been multiple iterations of the rotator controller design, but the modularity of the approach enables operations between different versions of the controller and the rotator. Since the start of 2016, the rotator controller design is able to facilitate a DC-motors or stepper-motors rotator design. We intend to keep this modularity for the electronics and firmware design to facilitate the variety of build by our community.
Rotator Controller v2
The PCB are tested in this ground station.
Features
- It is designed to fit the entire electronics needed to control rotator in Euroboard 80x50 mm.
- Main micro-controller is Arduino pro-mini, SparkFun's Arduino Pro Mini 328 dev-board with ATmega328p.
- The modular design includes plug-in either DRV8825/A4988 or DC motor drivers (MC33926).
- The power supply in embed in the same board in contrast with previous version.
- Filtered power supply of micro controller.
- An I2C multiplexer is used to connect I2C encoders AS5601 (same ID) to get position feedback for each axis.
- A temperature sensor TC-74 monitoring the temperature inside the controller box in order to protect them from over-heating.
- There are some spare dev-pins in order to connect other peripherals like IMU or an LCD display.
- Pins with integrated RC-Low Pass filter for end-stops connection.
- Default communication interface is RS-485 but it can also be used as a UART.
- Using different paths for digital and power (motors) GND.
- Electrolytic capacitor and TVS-diode in PSU input
- Flashed either by using UART or ISP header
Build sequence
- Make sure you have a mechanical assembly of the rotator constructed and ready
- Buy the PCB. OshPark,Seeed FusionPCBWay.com, DirtyPCBs.com, Elecrow, Makerfabs have been used in the past with good results.
- You can order the v2.2 of the board directly using this OSHPark link
- You can order the v1.0 of the rotary encoder board using this OSHPark link
- You can order PCB as well as PCB Assembly service from Seeed Studio
- Get all the necessary components according to BOM from latest tag (or the version that you want to build), Gitlab Tags
- Assemble the PCB, by soldering the components
- Burn the firmware
- Using the wiring diagram, connect the controller to the Rotator
- You are ready! Proceed with testing
Assembly Guide
Microcontroller
The main micro-controller of the board is arduino pro-mini 5V@16MHz, ATmega328P. The +5V of the controller are produced from arduino pro-mini. Some clones do not use correct parts in LDO, like the original one, with result, when it powers up with +12V, burned.
Some examples,
One Solution is not use clones, use Sparkfun's arduiuno pro-mini 5V@16MHz, ATmega328P. The second solution is to add a LDO, like MIC5205 (maybe in a new revision of v2).
The power consumption in +5V is:
- | QTY. | VCC(V) | IDD(mA) | Total(mA) |
---|---|---|---|---|
AS5601 | 2 | 5 | 6.5 | 13 |
PCA9540B | 1 | 5 | 0.1 | 0.1 |
SN65HVD485E | 1 | 5 | 2 | 2 |
TC74 | 1 | 5 | 0.35 | 0.35 |
arduino pro mini | 1 | 5 | 20 | 20 |
MC33926 | 2 | 5 | 0.2 | 0.4 |
DRV8825 | 2 | 5 | 0.1 | 0.2 |
The LDO MIC5205 guaranteed 150mA output, for Stepper motors ~35-40mA, for DC motors ~35-40mA.
Motor Drivers
Stepper motor driver
For the stepper motor driver 2 options have been tested, DRV8825 and A4988. For both options it is necessary to solder:
- 2 electrolytic capacitors C3, C4 100uF
- 4 single 0.1" male connectors for U3, U4
- 2 fixed terminal blocks P7, P8, Amphenol-VI0421550000G
- 6 jumpers to adjust the micro-step, default option is Full Step
Note: Guide for microstepping selection
JP3/JP6 | JP2/JP5 | JP1/JP4 | Microstep Resolution |
Low | Low | Low | Full step |
High | Low | Low | Half step |
Low | High | Low | 1/4 step |
High | High | Low | 1/8 step |
Low | Low | High | 1/16 step |
High | Low | High | 1/32 step |
Low | High | High | 1/32 step |
High | High | High | 1/32 step |
- DoNOT solder 2 resistors 100k, R4, R7 in default configuration (full step)
- If you have A4988 for stepper motor drive and you want to use micro stepping, when the MS1 is HIGH
it is necessary to solder R4, R7 according to A4983 Stepper Motor Driver Carrier, Step (and microstep) size.
In case of DRV8825, all pins MS1, MS2, MS3 have internal pull-up resistor.
Also it is necessary to update the definitions in firmware, according to microstepping selection. Example:
- Step Angle: 1.8 deg
- Microstep: 1/8 step
- Steps per Revolution: (360/1.8)*8 = 1600
That means:
#define MICROSTEP 8 ///< Set Microstep #define MAX_SPEED 6400 ///< In steps/s, consider the microstep #define MAX_ACCELERATION 1600 ///< In steps/s^2, consider the microstep #define SPR 1600L ///< Step Per Revolution, consider the microstep
It is necessary to change the maximum speed and acceleration according to new SPR.
An example:
The speed = 300steps/s and acceleration = 100steps/s^2 with
- 1.8 deg/step stepper motor
- full step
- gear ratio 54
means speed = 10deg/s and acceleration = 3.3deg/s^2 according to this function.
Be careful:
- adjust the current (current limiting) for stepper motors
- add a heat-sink.
- plug the stepper motor drivers
The stepper motor that is used, is Nema 17 Bipolar 59Ncm,
- Size: ▱42 x 48 mm
- Weight: 390 g
- Shaft diameter: 5 mm
- Step Angle: 1.8 deg
- Nominal speed @ 12V: 720deg/s
- Rated Current/phase: 2.0A
- Stall torque @ 12V: 0.59Nm
DC motor driver
It is necessary to solder:
- Solder U6 with 0.1" female connectors as shown in picture
- Solder 2 pads in yellow circle by using ~1mm diameter wire
- Solder 2 2-pin 3.5mm terminal blocks for 2 DC motors
Make sure you have not soldered the 2 electrolytic capacitors C3, C4 100uF. Those are only needed for the stepper motors. They can be destroyed by the DC motors and cause a short circuit of the power supply.
The DC motor controller is Dual MC33926 Motor Driver Carrier
- Motor driver: MC33926
- Motor channels: 2
- Minimum operating voltage: 5V
- Maximum operating voltage: 28V
- Operating voltage: 12V
- Continuous output current per channel: 2.5A
- Current sense: 0.525 V/A
- Maximum PWM frequency: 20 kHz
- Operating PWM frequency: 3921.5Hz (~4kHz)
- Minimum logic voltage: 2.5V
- Operating logic voltage: 5V
- Maximum logic voltage: 5.5V
The DC motor that we use is 50:1 Metal Gearmotor 37Dx54L mm,
- Size: 37D x 54L mm
- Weight: 195 g
- Shaft diameter: 6 mm
- Free-run speed @ 12V: 200 rpm
- Free-run current @ 12V: 300 mA
- Stall current @ 12V: 5000 mA
- Stall torque @ 12V: 1.2Nm
Communication
Note: For both options the firmware is the same.
UART
To use UART:
- solder JP7 and JP8
- solder pin header 0.1" female connector
- not solder C1, U2, R18, R19 R9, R8, R1, D3
- A is TX and B is RX
RS-485
To use RS485:
- solder pin header 0.1" female connector
- solder C1, U2, R18, R19 R9, R8, R1, D3
- not solder JP7 and JP8
If you use PCB without R19 footprint, you can add it in arduino pro-mini UART header.
Power Supply
Recommended power supply for rotator controller is: 48V @ 1A DC. A good choice is the MEAN WELL LRS-50-48
The switching power supply could get as input voltage, 19-60V DC.
In different input voltages, must be change the components like D4 and F1.
Default PCB components works at 48VDC.
Endstops
In reference design, mechanical endstops (the P/N SS0505 of endstop is specified in satnogs rotator BOM) , are used.
The controller has the capability to accommodate optical or magnetic endstop which connected to P2 header with silkscreen, SW1, SW2, +5V and GND.
Mechanical endstops are connected to
- SW1 and GND for azimuth axis
- SW2 and GND for elevation axis
Encoders
Source files: satnogs-rotator-controller-encoder - GitLab Firmware: satnogs-rotator-firmware - GitLab
For stepper motor setup is optional (AS5601 encoder).
For DC motor setup is necessary.
Fabrication files are placed in latest tag of satnogs-rotator-controller-encoder - GitLab.
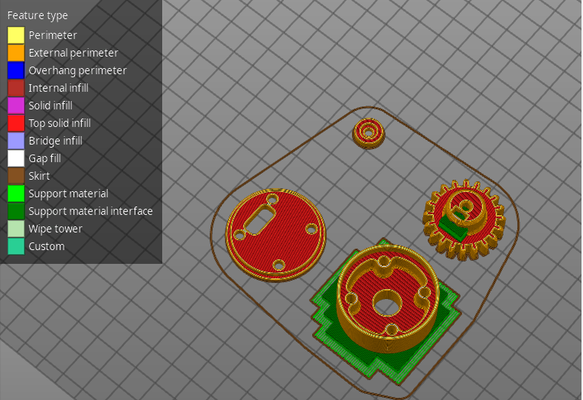
Firmware and Pin Assignments
Firmware
For stepper motors
For DC motors, thanks to ph4as
Pins Configuration
This configuration is from the latest release in Rotator Controller repository
- M1IN1 10, Step or PWM1
- M1IN2 9, Direction or PWM2
- M1SF 7, Status flag
- M1FB A1, Load measurment
- M2IN1 11, Step or PWM1
- M2IN2 3, Direction or PWM2
- M2SF 6, Status flag
- M2FB A0, Load measurment
- MOTOR_EN 8, Enable/Disable motors
- SW1 5, Endstop for axis 1
- SW2 4, Endstop for axis 2
- RS485_DIR 2, RS485 Half Duplex direction pin
- SDA_PIN 3, Data I2C pin
- SCL_PIN 4, Clock I2C pin
- PIN12 12, Digital output pin
- PIN13 13, Digital output pin
- A2 A2, Analog input pin
- A3 A3, Analog input pin
Pre-Flight Check
- Power your PCB with 48VDC, without plug-in arduino pro-mini and motor drivers, measure with multimeter the voltage in point 1. Expected voltage +12V (reference to GND).
- Plug arduino pro-mini and measure with multimeter the voltage in point 2. Expected voltage +5V (reference to GND).
- Plug motor drivers (for steppermotors ensure the current is adjusted properly)
- Connect all peripheral devices like motors, sensors, endstops
If the two first steps fail, something is wrong (maybe there is a short circuit) in PCB. Check the connections with a multimeter.
Then the board is ready to run the firmware, satnogs-rotator-firmware.
Wiring
The silkscreen of PCB shows where the end-stops, rotary encoders, motors and communication interface are connected. For example SW1 is referred to azimuth end-stop, I2C-1 to elevation rotary encoder and M1 to azimuth motor. An example of wiring with SatNOGS Rotator v3.
Troubleshooting hints
As soon as the board is powered up or reset, it will auto-home, on first build you can trigger a reset multiple time or move the homing ring to get it "home".
Connecting directly to the Arduino pro-mini you will need to use 19200 bauds and "newline" line ending.
Here is some commands (took from [1]) you can issue in the terminal emulator of your choice to test things:
- VE, it will returns something like "SatNOGS-v2.0"
- RESET, move to home position
- AZxx, ELxx, move to specified position (number)
Nothing moves ? Look at the status and error register :
- GS, status register : 1 idle, 2 moving, 4 pointing, 8 error
- GE, error register : 1 no error, 2 sensor, 4 homing, 8 motor, 12 over temperature, 16 watch dog timer interrupt
By example, at first start, you might be in GS8 and GE4 until you get a good homing position for the rotator to start working.
If you using an unreleased version of the board (the board that has fuse holder), in community post you can find pin configuration file.
Rotator Controller v1